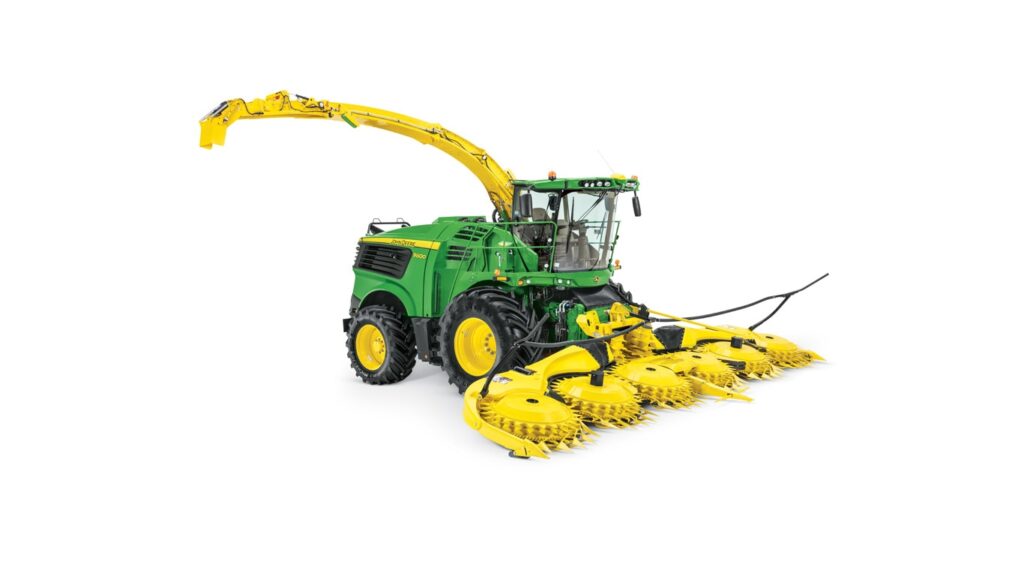
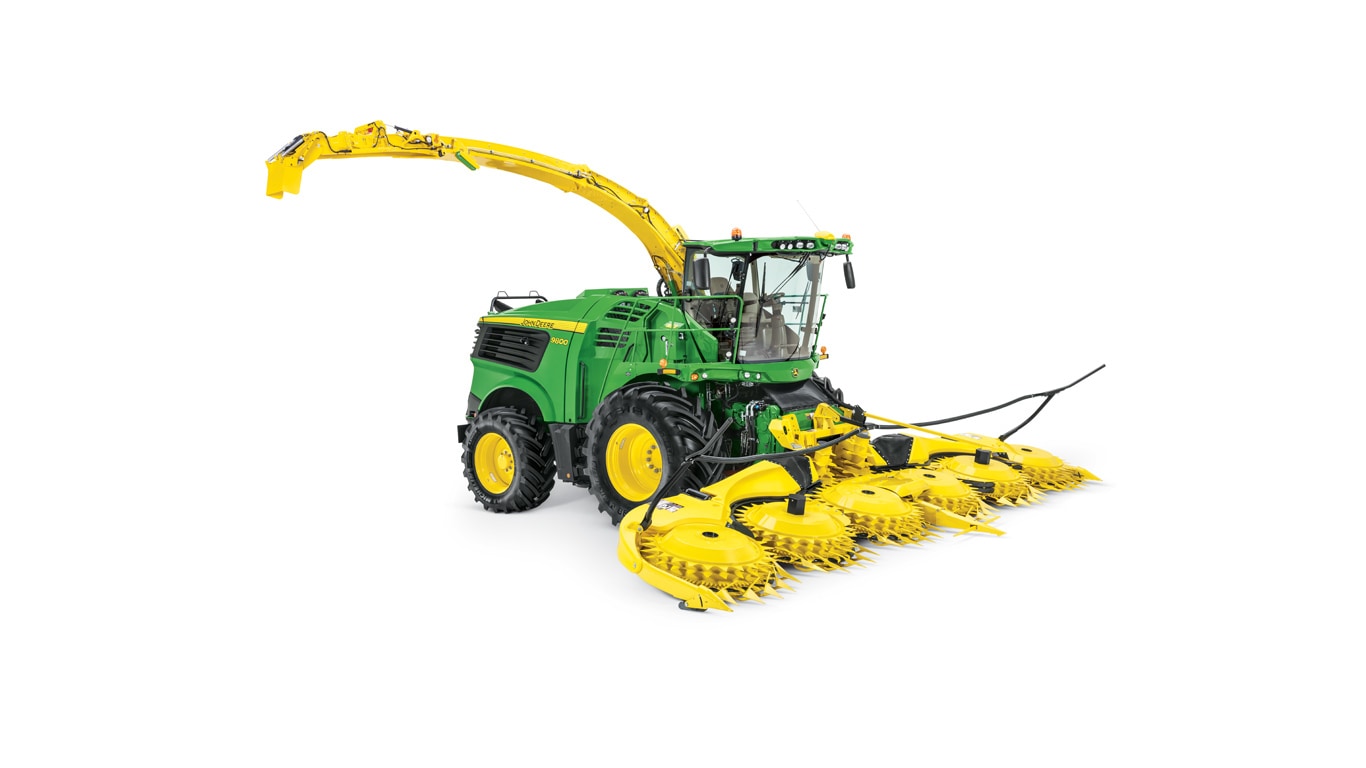
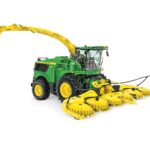
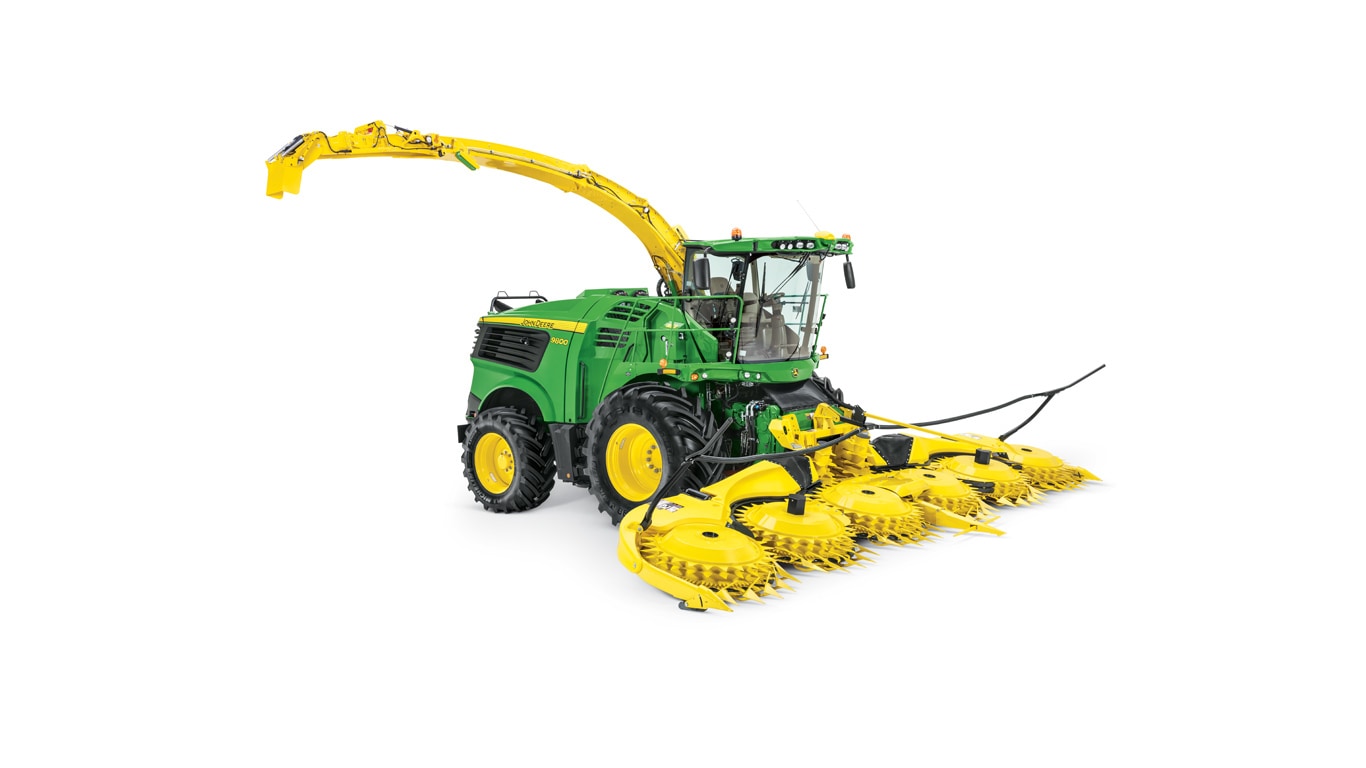
John Deere 9800 Self-Propelled Forage Harvester
Agriculture
- 856 hp, 24L Liebherr V12 engine
- Driveline designed to deliver optimal crop flow when the engine is operating in its efficiency sweet spot
- The ProStream crop flow designed with extra heavy-duty components for high horsepower and more throughput than ever before
Cutterhead - Speed at rated engine speed | Standard - 1170 rpm Optional - 1350 rpm |
---|---|
Blower/Crop accelerator - Number of blades | 10 |
Cab - Cool box | Optional |
Key Specs - Fuel system | Common rail plus four valves |
Engine - Fuel system | Common rail plus four valves |
Feeding system/Feedrolls - Width, front | 830 mm 32.7 in. |
Electrical system/Electrical and hydraulic system - Type/voltage | 12 / 24 V |
Driveline - Belt tensioning | Active, hydraulic pressure |
Electrical system/Electrical and hydraulic system - Hydraulic system capacity | 50 L 13.2 U.S. gal. |
Cab - Hectare counter | Standard |
Feeding system/Feedrolls - Feed roll frame opening | Swing away, 37-45 degree (angle) |
Cutterhead - Knife types available (crop) | Straight - grass Curved - corn |
Cooling system - Cooling fan drive | Direct |
Ground drive - Automatic wet brake system | Standard |
Cab - Side window wiper | Rear and side window wiper optional Parallel-type windscreen wiper |
Key Specs - Fuel tank capacity | 1,500 L 396.3 U.S. gal. |
Cab - Tilt and extend steering column | Standard |
Driveline - Main clutch | Dry clutch |
Spout - Rotation, degrees | 210 degree (angle) |
Driveline - Number of discs | Two discs |
Spout - Double-cap deflection | Standard |
Vehicle - Transport length (without header) | 6.6 m 21.7 ft |
Engine power - Fuel tank capacity | 1500 L 396.3 U.S. gal. |
Ground drive - Differential lock | Manual and automatic |
Engine - Displacement | 24.2 L 1476.8 cu in. |
Feeding system/Feedrolls - Number | Four |
Driveline - Hydraulics | Load sensing |
Cutterhead - Knife drum width | 850 mm 33.5 in. |
Engine - Model | D9512 A7 04 |
Cab - Trainee seat | Standard |
Maintenance - Engine oil and filter change duration | 1000 hours |
Maintenance - Rotary radiator screen cleaner | Standard |
Engine - Cylinders | V 12 |
Cab - Operator information system | Cornerpost display |
Electrical system/Electrical and hydraulic system - Batteries/battery quantity/capacity | 3 x 174 amp-hr |
Knife sharpening system - Reverse rotation | Yes |
Knife sharpening system - Automatic from cab | Yes, remote from cab |
Kernel processor - Quick-change | Quick kernel processor - swing in/swing out |
Blower/Crop accelerator - Speed (option) | 1890 rpm |
Kernel processor - Quick KP removal | Optional crane with remote-controlled electric hoist |
Machine management solutions - Yield monitoring | Harvest Monitor™ optional |
Header connection - Header height control | Advanced header control (AHC) optional |
Cutterhead - Shear bar options | Grass, corn, Dura Line™ corn, Dura Line Plus |
Machine management solutions - Assisted steering systems | Optional: AutoTrac™, Manual RowSense™, AutoTrac RowSense, Machine Sync |
Cab - Air conditioning and heater | Standard: ClimaTrak™ control |
Feeding system/Feedrolls - Stone detector | Optional |
Maintenance - Automatic lubrication system | Standard: AutoLube |
Key Specs - Engine | Type Liebherr® Exhaust emission regulation compliancy: Final Tier 4 / EU Stage V Displacement 24.2 L 1476.8 cu in. Model D9512 A7 04 Cylinders V 12 |
Harvest channel - Width | Wide body channel |
Engine - Type | Liebherr Exhaust emission regulation compliancy: Final Tier 4 / EU Stage V |
Header connection - Maize headers | 8, 10 or 12 rows Working width: 6, 7.5, or 9 m 19.7, 24.6 , or 29.5 ft |
Engine power - DEF tank capacity ( for FT4 or EU Stage V emission level) | 103 L 23.8 U.S. gal. |
Header connection - Auto PTO coupler | Optional |
Header connection - Grass pickups (transport width) | 3, 4, 4.5 m 9.8, 13.1, 14.8 ft |
Header connection - Infinitely variable header drive | Standard |
Key Specs - Maximum power | At 1800 rpm (ECE R120): 640 kW 870 PS / 858 hp |
Driveline - Ground drive | ProDrive™ system, autoshift transmission, differential lock (automatic and manual), automatic wet brake system Engine rpm on road: 1200-1800 rpm |
Vehicle - Transport height (to cab roof) | Below 4 m 13.12 ft |
Ground drive - Rear axle type | Hydromechanical 4WD |
Knife sharpening system - Sharpening modes | Grinding and finishing |
John Deere Premium KP - Lubrication | Grease |
Machine management solutions - Documentation | Harvest Doc™ optional |
Driveline - Main driveband, polybelt belts | Nine grooves |
Header connection - Multicoupler | Standard |
Cab - Electric adjust and heated | Optional on rearview mirrors |
Cab - Panoramic view windows | Standard |
John Deere Premium KP - Housing | Standard KP housing |
John Deere Premium KP - Maize - standard sawtooth or Dura Line™ roll teeth number (speed differential) | 118 (32 or 40 percent) |
Cab - CAN bus electronics | Standard |
John Deere XStream KP - Lubrication | Pressurized oil |
Cutterhead - Knife drum diameter | 670 mm 26.4 in. |
Machine management solutions - Length-of-cut control based on crop parameter | Standard: Infinitely variable length-of-cut (IVLOC™) Optional: AutoLoc™ system - use with HarvestLab |
Header connection - Lateral pivoting frame | Standard |
Vehicle - Transport width (without header) | 3.2-3.8 m 10.5-12.5 ft |
John Deere Premium KP - Roll diameter | 240 mm 9.45 in. |
John Deere Premium KP - Weight | 163.3 kg 360 lb |
Cutterhead - Type | Dura-Drum™ cutterhead |
Driveline - Main driveband | Reinforced with Kevlar® inserts |
John Deere XStream KP - Housing | Heavy-duty KP housing |
Harvest channel - Crop flow components | Low-friction crop flow concept |
Feeding system/Feedrolls - Metal detector | Standard |
Machine management solutions - Crop analysis | HarvestLab™ 3000 optional |
Blower/Crop accelerator - Rotor diameter/housing width | 560 / 620 mm 22.86 / 24.41 in. |
John Deere XStream KP - Maize - Dura Line sawtooth or XCut roll teeth number (speed differential) | 110/145 (50 percent) |
Spout - Reach from center line (Optional) | 6 or 8 row: 4.73 m 15.5 ft 10 row: 5.87 m 19.3 ft 12 row: 6.71 m 22 ft |
Key Specs - DEF tank capacity ( for FT4 or EU Stage V emission level) | 103 L 23.8 U.S. gal. |
Cab - Operator's seat | Standard: Air-suspension seat |
Kernel processor - Type | John Deere Premium KP™, John Deere XStream KP™ |
Cab - Rearview mirrors | Standard |
John Deere XStream KP - Whole crop - Dura Line XCut roll teeth number (speed differential) | 145/165 (50 percent) |
John Deere XStream KP - Roll diameter | 250 mm 9.8 in. |
Electrical system/Electrical and hydraulic system - Alternator | 12 V - 200 amp 24 V - 140 amp |
Spout - Working height (maximum) | Height to spout: 6.6 m 21.65 ft |
Engine - Air compressor | Base |
Header connection - Header drive | Base: Heavy-duty gearbox (i=3.75); pump/motor displacement: 85/80 cc Optional: Extra heavy-duty gearbox (i=4.31); pump/motor displacement: 110/90 cc |
Ground drive - Maximum transport speed | ProDrive system: 20/25/30/40 km/h 12.4/15.5/18.6/24.9 mph |
Feeding system/Feedrolls - Standard feedroll drive | Hydro feedroll drive IVLOC Infinitely header drive speed |
Engine power - Maximum power | At 1800 rpm (ECE R120): 640 kW 870 PS / 858 hp |
Spout - Hydraulic height position | Standard: Hydraulic raise and lower Optional: Automatic spout positioning |
John Deere Premium KP - Whole crop - standard sawtooth roll teeth number (speed differential) | 178 (32 or 40 percent) |
Ground drive - Engine speed management | Standard |
Featured List
- Channel Width: Wide
- Fuel Tank Capacity: 396 gal. (1500 L)
- Engine: Liebherr
- Displacement: 24 L
- Rated Power: 856 HP
Featured Content
The John Deere 9000 Series Self-Propelled Forage Harvesters (SPFH) have been developed with a clear focus on machine performance: more throughput and less fuel consumption while providing maximum uptime and low cost of operation.
A key success factor is the concept of lower engine rpm at higher harvesting component speeds.
V12 – 24-L concept: The Liebherr® D9512 engine
The top-model 9700, 9800, and 9900 SPFH are equipped with a Liebherr 12-cylinder V-engine with 24-L displacement. The Liebherr D9512 is a state-of-the-art engine and delivers what a high-performance forage harvester requires:
- High power density and great fuel efficiency
- Constant maximum power down to lower engine rpm
- Torque curve designed for forage harvesting applications
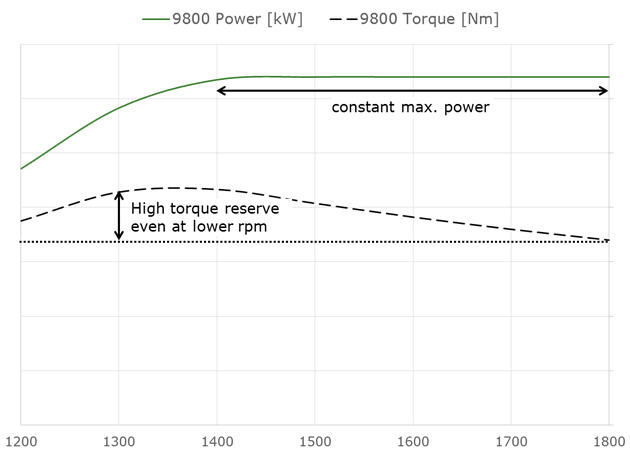
Torque and power of the Liebherr engine
The broad maximum power range of the Liebherr V12 engine cuts off the less-efficient rpm area above 1800 rpm. The rising torque curve down to 1300 rpm enables efficient operation of the machine in the lower rpm range.
Revised driveline with optimized component speeds
To reach maximum efficiency and performance, all machine component speeds are re-worked and laid out for best function in the 1400 to 1800 engine rpm range. This also leads to better fuel efficiency with an optimum range from 1250 to 1600 rpm, where the engine has its lowest specific fuel consumption (g/kWh).
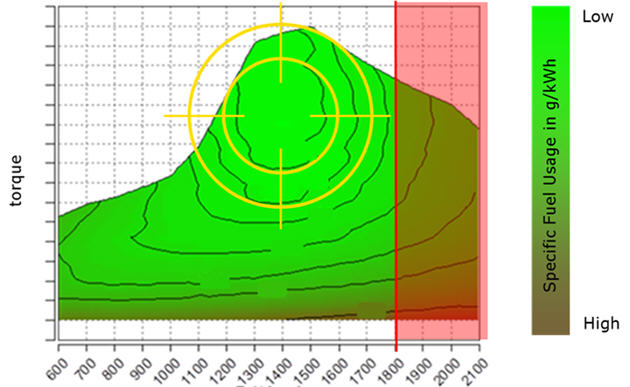
Specific fuel usage in rpm range
This unique concept delivers undisputed customer value:
- 10 percent more throughput (t/kW)*
- 10 percent better fuel economy (L/t)*
- More hours in the field with 1500-L (396.25-gal.) diesel tank and 90-L (23.8-gal.) urea tank
*Compared to replaced models
Liebherr is a trademark of Liebherr-International AG.

HarvestLab 3000 measures dry matter and constituents on the go
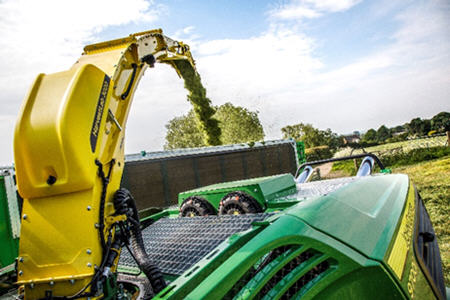
HarvestLab 3000 sensor mounted on the spout
The HarvestLab 3000 sensor mounts to the top of the discharge spout and takes accurate dry matter and ingredient readings (more than 4000 measurements per second) of the crop through the sapphire glass lens as crop passes through the spout. This is the same technology forage labs use to measure dry matter. HarvestLab 3000 with John Deere Constituent Sensing measures dry matter and constituents like sugar, starch, acid detergent fiber (ADF), neutral detergent fiber (NDF), crude fiber, crude ash, crude protein, crude fat, Metabolic Energy and ELOS depending on the crop. In addition, the HarvestLab 3000 sensor can also be used as a stationary unit.
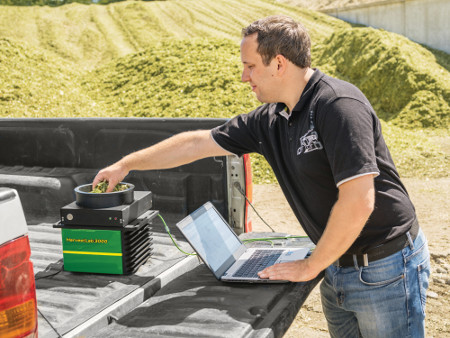
Stationary usage of HarvestLab 3000
Crop type and constituent sensing
Crop type | Moisture/ dry matter | Crude protein | Crude starch | uNDF | ADF | Crude sugar | Crude Ash |
Corn | X | X | X | X | X | — | X |
Alfalfa | X | X | — | X | X | X | X |
Whole crop silage | X | X | X | X | X | X | X |
Grass | X | — | — | — | — | — | — |
When HarvestLab 3000 is used in conjunction with Harvest Monitor™ system, a wealth of important information becomes available to the operator, including productivity in acres per hour, throughput in tons per hour, total area harvested, total crop mass harvested, yields, and dry matter. To measure and document the constituents, a Gen 4 4640 Universal Display is required. All data documented on the Gen 4 4640 Universal Display is shown in John Deere Operations Center.
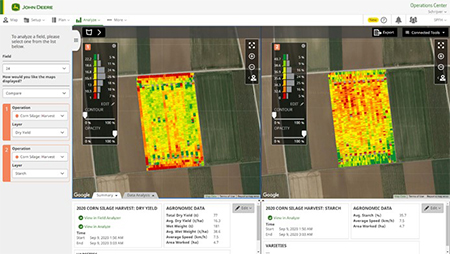
Constituent data in Operations Center
When the HarvestLab 3000 is used in conjunction with an 8000 or 9000 Series Self-Propelled Forage Harvester (SPFH) and a GreenStar™ display, AutoLoc functionality is automatically present. AutoLoc automatically varies the length of cut according to the desired crop-dry matter correlation settings based on the dry matter readings from the HarvestLab 3000 sensor. With the AutoLoc adjustment, bunk density is improved and a high forage quality is reached.
AutoLoc – Automatic length of cut
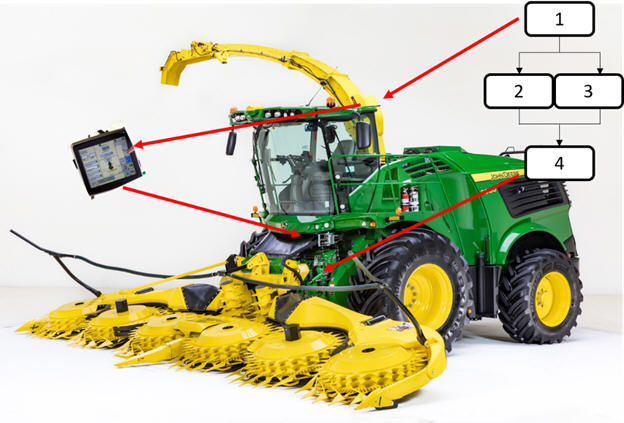
AutoLoc on the SPFH
- HarvestLab 3000 — moisture and ingredients on the go
- Manual control (operator)
- AutoLoc — automatic control
- IVLOC™ transmission — length of control changes on the go
AutoLoc, a feature exclusive to John Deere and unique to the market, brings added value to the HarvestLab sensor and John Deere SPFH. AutoLoc works in conjunction with the HarvestLab 3000 sensor and IVLOC transmission to automatically adjust the length of cut (LOC) based on crop moisture levels to improve bunk density and reduce long particles in dry corn. Nutritionists, herdsmen, and SPFH operators will all benefit from this innovation.
John Deere is leading the industry in providing real-time information that matters most to forage production. Quality forage comes from properly packed silage, which is directly related to the moisture content and LOC of the crop.
LOC changes are made automatically in the field based on moisture readings and predetermined settings determined by operator requirements. No in-field calibration is required to load the LOC requirements; the operator simply uses the GreenStar™ display to program the desired LOC settings at different moisture levels.
When moisture levels of crop in the field change, the IVLOC drive automatically responds to either increase or decrease the feedroll speed, which in turn changes the LOC. If moisture levels of the crop are outside of the desired range, the IVLOC transmission adjusts and limits the LOC based on the maximum and minimum LOC settings as determined by the operator.
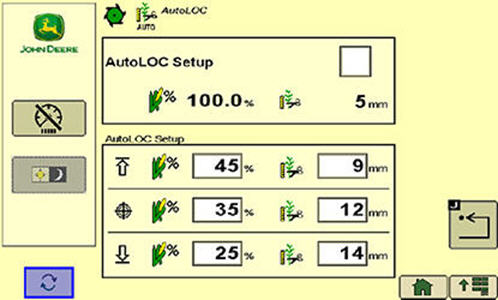
AutoLoc screen
AutoLoc solves the dry matter and LOC puzzle
According to the accurate moisture readings, AutoLoc is able to adjust the proper LOC automatically in steps as small as 1 mm (0.04 in.). This process is faster and more accurate than any operator could do manually because of all the other important operating functions being performed. This can increase overall efficiency dramatically.
With AutoLoc, the SPFH operator simply sets the minimum, optimum, and maximum moisture levels and the corresponding lengths of cut. AutoLoc then creates a linear curve between the minimum and the optimum and between the optimum and the maximum. LOCs are then determined based on those lines.
For example, if the optimum LOC were set to 15 mm (0.59 in.) at 68 percent moisture and 8 mm (0.31 in.) at 50 percent moisture, and the actual moisture of the crop was 63 percent, AutoLoc would change the LOC to be 13 mm (0.51 in.) based on the linear curve it created.
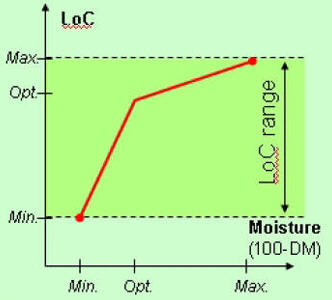
AutoLoc chart
Forage harvester performance and AutoLoc
The following equipment is required for AutoLoc functionality:
- GreenStar display with Gen 4 4640 Universal Display
- HarvestLab 3000 sensor
- 8000 or 9000 Series SPFH
Why AutoLoc is a must to ensure silage quality and overall profitability
It impacts the silage compaction in the bunker to ensure the quality of feed being stored is the best quality possible.
Silage density and AutoLoc
Good silage starts with high bunk density to preserve the crop value. This is the main objective for both dairy/beef producers and biogas plants. Many factors are involved in achieving high bunk density, including type of crop, moisture levels, length of cut, bunk filling speed, and compaction machinery.
Some of these factors cannot be easily changed while harvesting. AutoLoc adds an improved sense of control to the harvesting and silage storage operation. Operators do not need to compromise when choosing the proper length of cut based on moisture. AutoLoc takes care of this chore automatically.
Oftentimes, producers are so focused on getting the job done that important tasks and details are overlooked during the harvesting operation. Knowing the growing period for corn silage covers five months growing in the field and only a few days harvesting for 10 to 12 months of feeding, the process of the silage harvest and storage should be managed as well as possible.
The impact of the silage quality, which can be harvested and stored in just a few days, can have a huge impact on income throughout the entire year. The silage cost is a major part of the expenses in the dairy/beef and biogas plant businesses. Poor forage quality can cost tens of thousands of dollars per year in increased feed costs resulting in the producer having to invest in additional silage to reach the desired feed ration.
Spoilage/reheating and seeping losses are the biggest problems in silage bunks. These problems often happen due to insufficient compaction and an incorrect LOC. To achieve the right amount of silage compaction and keep as much air out of the silage as possible, the LOC has to be adjusted according to the moisture levels of the crop – the wetter the material, the bigger the particle size.
While varying lengths of cut can dramatically help to achieve high density levels, the length of cut of the material must be consistent in order to maintain normal rumination, chewing, and saliva production in the rumen. If the particles are too small, the food does not fit anymore with the process of the cow rumen and the compaction becomes difficult due to the instability of the material.
For this reason, John Deere created AutoLoc, which automatically adjusts the length of cut to the moisture value, while staying within the preset LOC range.
Having some limited LOC variations in a bunk silo should not affect the effective fiber in the ration on a daily basis. Using AutoLoc in conjunction with upright or bag silos can vary the effective fiber fed to animals on a daily basis.
Looking at the studies done by Honig and Rohr in 1985, as can be seen in the following table, it is possible to get high-density levels of dryer crop when the crop is chopped at a shorter LOC.
Length of cut |
Bunk density |
|
73 percent moisture |
64 percent moisture |
|
4 mm (0.16 in.) |
205 kg/m3 (12.8 lb/cu ft) |
179.7 kg/m3 (11.2 lb/cu ft) |
7 mm (0.28 in.) |
192.2 kg/m3 (12.0 lb/cu ft) |
174.6 kg/m3 (10.9 lb/cu ft) |
14 mm (0.55 in.) |
173 kg/m3 (10.8 lb/cu ft) |
157 kg/m3 (9.8 lb/cu ft) |
Leading header technology
John Deere rotary harvesting units are built for reliable and powerful feeding of high-capacity forage harvesters. Two fundamental designs are available to match all producer needs. The 600plus Series Headers are the universal solution for different crops up to 4-m (13.1-ft) tall. The 700plus Series Headers are the perfect solution for high-yielding crops.
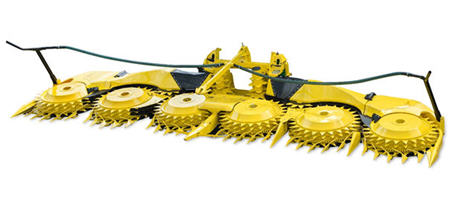
772 Rotary Harvesting Unit
Available beginning in model year 2019, the top-model 772 12-Row Large-Drum Rotary Harvesting Unit has been designed to fully leverage the capacity of 9000 Series Self-Propelled Forage Harvesters (SPFH).
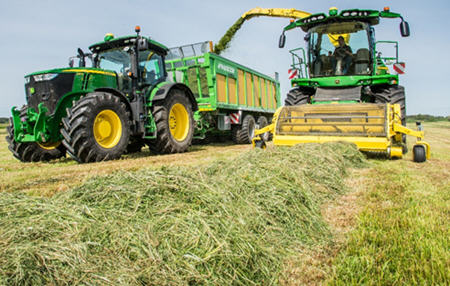
6X9 Series Windrow Pickup
The 6X9 Series Pickups with the patented endless flight vortex auger design and optional dual header drive enable high-capacity feeding of John Deere SPFH. Key advantages are the throughput boost in high-yielding crops but also the easy handling of uneven windrows.
Variable header drive
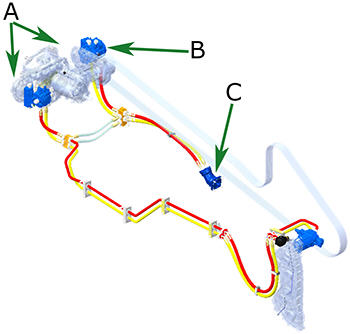
Power distribution gearbox (A), header pump (B), and header motor (C)
John Deere SPFH come with variable header drive in base. The header speed is automatically synchronized with the feeding speed and length of chop through a hydrostatic IVT™ drive system. This ensures a gentle and even crop transfer from the header into the machine without blocking or disrupting material transition. Producers receive the benefit of high chopping quality and full leverage of the header and crop flow potential.
Dual header drive
Dual header drive for the SPFH and the 6X9 Series Pickups complements the benefits of the variable header drive. While the variable header drive automatically synchronizes the pickup auger and harvester feeding speed, the dual header drive with its individual hydraulic drive of the pickup tines is speed matched with vehicle speed to ensure clean crop picking in changing conditions and windows.
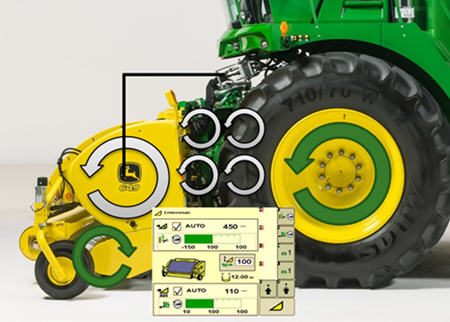
Speed synchronization between the SPFH and header
Tines speed up and slow down with forward speed while the pickup auger speed is still synchronized with the length of chop and feedroll speed. Producers benefit from a better quality of chop, smoother feeding, and an easy-to-utilize harvesting system.
Hydraulic feedroll dampening
The 9000 Series SPFH offer the hydraulic feedroll dampener in base. Next to the four individual springs applying high pressure on the crop mat entering the machine, the dampener supports crop compaction in uneven crop conditions and ensures smooth feeding even at the highest feeding speeds when chopping for a very long period.
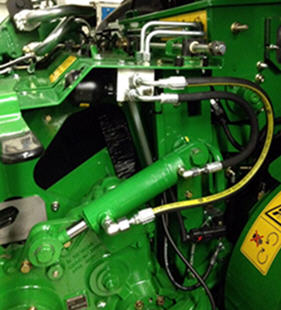
Hydraulic feedroll dampening
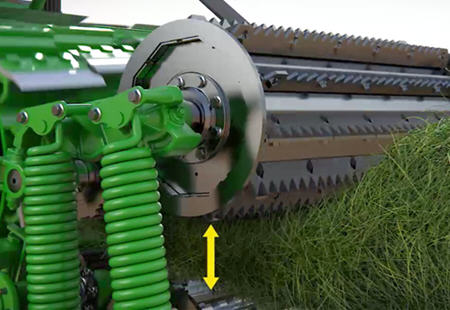
Crop compaction and even feeding at the feedroll
Unique foreign object protection
A state-of-the-art metal detector scans for metal in the crop mat and stops the intake in case of tripping. Optionally, this safety device can be completed with a unique stone detection feature that senses for knocks and abnormal feedroll movement. Two redundant sensors developed for this application improve solid foreign object detection and minimize false tripping caused by lumps or uneven windrows.
Overview
Due to increased machine usage (chopping more tons per hour), standard high-quality steel parts need to be replaced more frequently. Since 2010, John Deere has been meeting the challenge and exceeding expectations with Dura Line wear parts.
Dura Line components were developed by John Deere and are installed in high wear spots on the self-propelled forage harvesters (SPFH), mainly in the crop flow. The technology is normally used for heavy-duty environments such as mining and machine tooling. It is the highest material quality in the industry that is installed on an SPFH.
Benefits
- The coating is extremely wear resistant with an extraordinarily smooth surface due to the special heat treatment and a proprietary tungsten carbide composition.
- Dura Line™ provides a permanent fast-chopping process with low crop friction on the components while fuel consumption remains low.
- Tests show that when chopping in the same crop conditions and chopping the same tonnage, Dura Line parts last four times as long as, or longer than, standard parts. Time and money associated with replacing parts are significantly reduced.
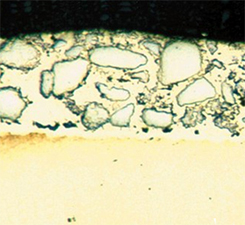
Dura Line coating
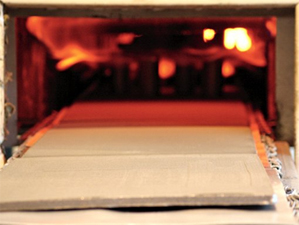
Dura Line processing
Additional details
Dura Line guarantee
The Dura Line guarantee provides a specified number of engine hours or time of usage (whichever comes first) for the different Dura Line liners. The Dura Line guarantee was first introduced in 2017 and is valid for all 8000 and 9000 Series SPFH models. Dura Line liners damaged from foreign material or misuse are excluded. Only parts that are completely worn are replaced.
For more information about the Dura Line guarantee, contact the local sales organization.
Dura Line packages
The John Deere Dura Line crop flow liners come in three packages. Depending on the individual harvesting requirements, there is a perfect package for every need.
- Basic: Perfect solution for machines mainly harvesting corn
- Premium: Ideal for abrasive conditions (particularly grass)
- Ultimate: Perfect choice for toughest conditions, providing full crop flow coverage
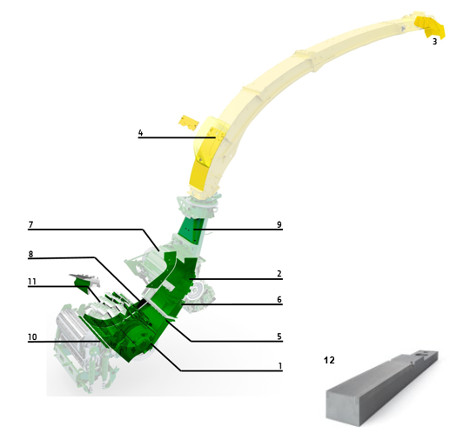
Dura Line wear parts
# | Dura Line component | Basic | Premium | Ultimate |
1 | Spiral band | √ | √ | √ |
2 | Accelerator band | √ | √ | √ |
3 | Spout flap | √ | √ | √ |
4 | Spout wear liners | √ | √ | |
5 | Front chute base liner | √ | √ | |
6 | Grass chute base liner | √ | ||
7 | Accelerator side wall liners | √ | ||
8 | Front chute side liners | √ | ||
9 | Transition front liners | √ | ||
10 | Dura Line™ smooth roll scraper | √ | √ | √ |
11 | Dura Line™ knife holder | √ | ||
12 | Dura Line™ Plus shear bar | √ | √ |
Overview
John Deere self-propelled forage harvesters (SPFH) set new standards in kernel processing performance. Proven in independent tests during corn harvest in 2016 and 2017, John Deere kernel processors (KP) deliver smashed kernels and highly processed plants that growers expect. With two different models, the John Deere Premium KP™ kernel processor and the John Deere XStream KP™ kernel processor, all different needs will be satisfied.
Additional details
All John Deere SPFH can be operated with or without a kernel processing unit in position. When not in use, a crop transition chute (or grass chute) swings into position with a few turns of a crank. The crop transition chute comes standard on all harvesters.
The SPFH feature the AutoLube central greasing harness; the respective central greasing equipment is available on the Premium KP kernel processor. The XStream KP kernel processor features automatic pressurized oil lubrication.
The John Deere Premium KP is available for the 9500 to 9800 models, and the John Deere XStream KP is available for all 9000 Series models. The 9900 model can only be equipped with an XStream KP.
John Deere Premium KP
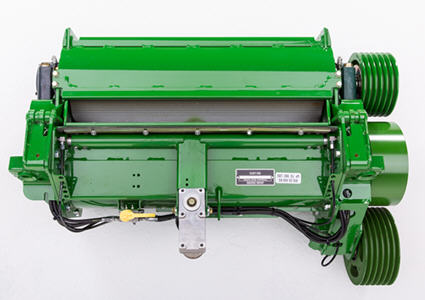
John Deere Premium KP kernel processor
On the 9000 Series, the proven John Deere Premium KP can be installed on the 9500 through 9800 models. With their highly intense processing, they deliver excellent forage quality at any length of cut.
The main features of the Premium KP are:
- 240-mm (9.45-in.) roll diameter for different crops (maize and whole crop)
- 32 percent speed differential; option of 40 percent speed differential
- Standard KP housing with grease lubrication in base
- Electric KP gap adjustment from the cab as option
The following rolls are available for the Premium KP:
- Standard sawtooth (118/118 teeth)
- Dura Line™ sawtooth (118/118 teeth)
- Whole crop sawtooth (178/178 teeth)
With the option of Dura Line rolls, a longer lifetime and less wear can be reached, resulting in lower cost of operation.
For easy and uncomplicated mounting and dismounting of the KP, a crane with electric winch can be installed as an option.
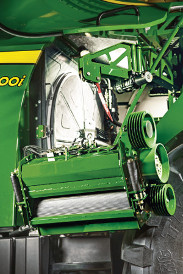
Mounting and dismounting the KP with the optional crane and winch
The following diagram shows the complete John Deere Premium KP offering with all possible combinations.
![]() |
Sawtooth (118/118 teeth) – code 3734 |
|
John Deere Premium KP with:
|
Dura Line sawtooth (118/118 teeth) – code 3738 |
|
Whole crop sawtooth (178/178 teeth) – code 3743 |
The following additional options are also available for the Premium KP.
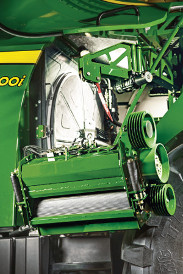
Crane for KP removal complete with electrical winch (code 8380)
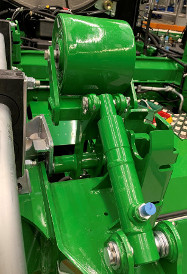
Hydraulic KP belt tensioner (code 8381)
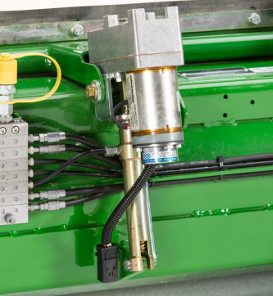
Electrical KP gap adjustment (code 8376)
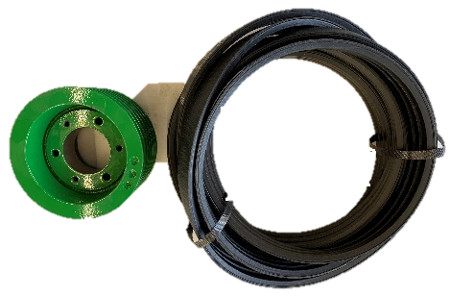
40 percent speed differential (code 9389)
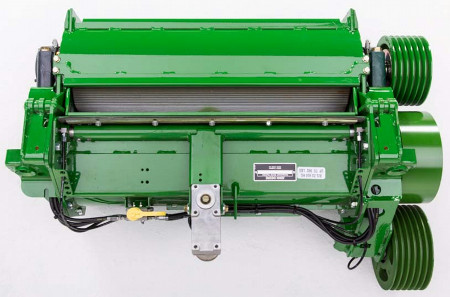
Complete whole crop KP as bundle (code 9379)
John Deere XStream KP
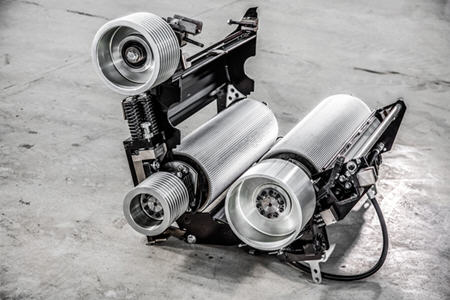
John Deere XStream KP kernel processor
The John Deere XStream KP is the heavy-duty solution made for high throughput and high-horsepower machines and stands for extreme processing at any length of cut in any crop and any conditions.
The XStream KP rolls are manufactured and delivered by Scherer Inc., located in South Dakota, United States. The kernel processor is supplied ex-factory by Scherer Inc. and fits on all 9000 Series models. As Scherer Inc. has a strong focus on dairy forage production and is the leading company in KP roll designs and manufacturing since 1999, a strong statement is set regarding kernel processing and forage quality.
More information about Scherer Inc. can be found on their website: http://www.schererinc.com/
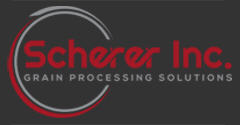
Scherer Inc. logo
The main features of the XStream KP are:
- 250-mm (9.8-in.) roll diameter
- 50 percent speed differential
- Heavy-duty housing with KP roll quick-exchange system
- Pressurized oil lubrication of bearings
- Bearing temperature monitoring system (option)
The following rolls are available for the XStream KP:
- Dura Line sawtooth (110/145 teeth)
- Dura Line XCut (110/145 teeth)
- Dura Line Whole Crop XCut (145/165 teeth) – only available for 9000 Series
All XStream KP options for 9000 series are available with 10- or 11-inch rolls.
In comparison to the Dura Line sawtooth rolls, the Dura Line XCut rolls have a spiral groove sawtooth profile that delivers excellent processing, especially at long lengths of cut. The spiral groove design delivers highly processed plants and smashed kernels.
For easy and uncomplicated mounting and dismounting of the KP, a crane with electric winch can be installed as an option.
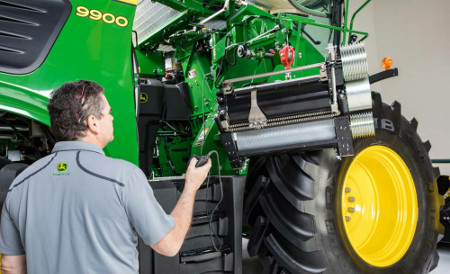
Mounting and dismounting the KP with the optional crane and winch
The following diagram shows the complete John Deere XStream KP offering with all possible combinations
![]() |
Dura Line sawtooth (110/145 teeth) – code 3750 |
|
John Deere XStream KP with:
Requires:
|
Dura Line XCut sawtooth with spiral groove (110/145 teeth) – code 3751 |
|
Dura Line XCut sawtooth with spiral groove for whole crop (145/165 teeth) – code 3752 |
The following additional options are also available for the XStream KP.
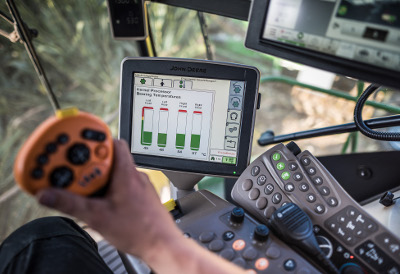
Temperature monitoring (code 838A)
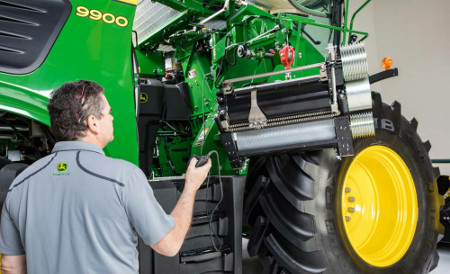
Crane for KP removal complete with electrical winch (code 8380)